Introduction
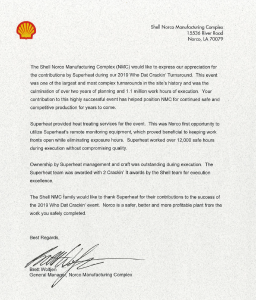
At Superheat, we believe Advancing Heat Treatment™ is more than just a catchy tagline. With innovative and technological advances, we strive to shift the ideology of what is possible within the industry. Superheat recently united one of the most accredited petrochemical producers, Shell Norco Manufacturing Complex (NMC), with Superheat SmartWay™, our patented approach to onsite heat treatment. As a result, Superheat received two awards for Execution Excellence during our contributions to the overall turnaround project. Shell Norco mentions, “Ownership by Superheat management and craft was outstanding during execution”.
Scope & Schedule
Superheat was chosen as the sole subcontractor for all of the on-site and off-site heat treatment needs during Shell Norco’s 2019 Who Dat Crackin’ Turnaround. It was one of the largest and most complex turnarounds in the site’s history – taking a culmination of over two years of planning. Superheat worked over 12,000 safe work hours and completed 1000+ heat treatment cycle applications, including: 3 Large Bore Vessels, 2 Fluid Catalytic Cracker Cyclone Heads, 2 Fluid Catalytic Cracker Cyclone cross-over duct work, and a variety of piping components throughout the facility. Superheat’s pre-project planning and execution ensured efficiencies in equipment and manpower throughout the job. This offered minimized risk, improved quality, saved time, and reduced costs at every stage of the project
Superheat SmartWay™ Advantage
Shell Norco explained that the key driver for success during the turnaround’s heat treatment was, “Superheat’s remote monitoring equipment, which proved beneficial to keep work fronts open while eliminating labor exposure hours”. The Superheat SmartWay™ integrates emerging communication technology (wireless and internet) and equipment advancements, with innovative software solutions to produce the most efficient, state-of-the-art, on-site heat treatment solution. Control room operators in the Superheat SmartCenter™ monitored Superheat SmartPoint™ equipment via a patented remote-monitoring process, ensuring that the onsite labor force was optimized, and heat cycle quality was maximized. The Superheat SmartCenter™ also provided the knowledge and design expertise necessary to efficiently set up and tear down heat treatment configurations to code and alignment with Shell Norco’s specific requirements for thermocouple distribution. The Quality Assurance Department ensured these specifications were met, and delivered the Superheat SmartReports™ electronically to Shell representatives.

Superheat SmartPoint™ offered flexibility and high zone control capacity which allowed us to be highly responsive to client needs and effortlessly adapt to project scope as it increased. Shell Norco also utilized the Superheat SmartView™ app, which provided one source of the truth regarding overall project data, more specifically quantitative heat treatment information in real-time via any device. In comparison to the traditional heat treatment process, Superheat SmartWay™ reduced the equipment requirements on the project by 75% and labor by 47% – a significant increase in efficiency.
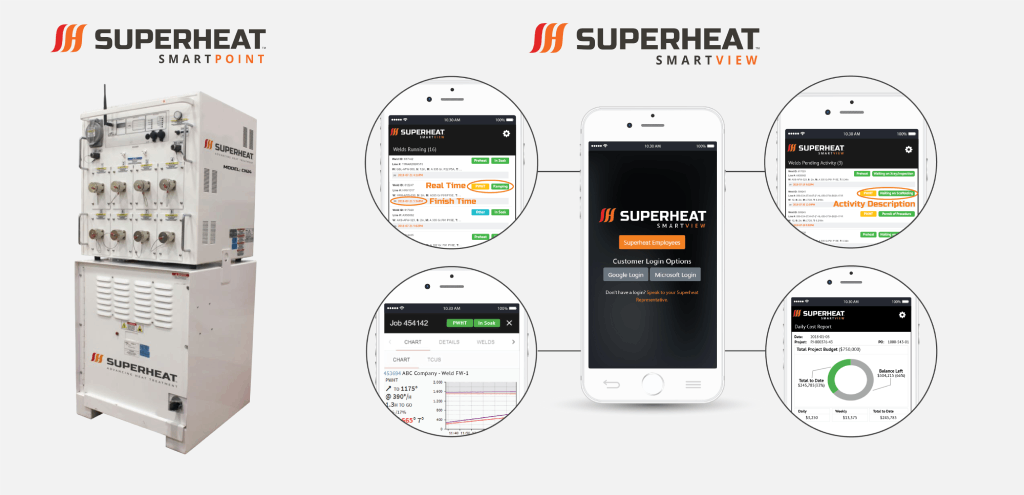
Results
In closing, Shell Norco stated, “Norco is a safer, better and more profitable plant from the work you safely completed”. Superheat not only appreciates this recognition but will use this project as a benchmark towards continual improvement. This latest achievement is a prime example of our standards as a global service leader and innovator within the industry. By providing A Smarter Way to Do Heat Treatment™, Superheat’s services are truly Better Safer Faster™.