Protect Your Schedule and Reduce Costs: The Hidden Truths of Heat Treatment
While often overlooked, the heat treatment process is a necessary element to the critical path construction and maintenance of various energy projects. If not completed with quality in mind, your project may be susceptible to delays and rework, ultimately dismantling your schedule and budget.
Thankfully there are a variety of ways you can ensure your heat treatment provider has the proper technology and procedures to prevent unnecessary rework. Choosing the right heat treatment service provider can also mitigate unforeseen demand spikes and reduce contractor labor costs from idle workers.
Heat treatment is required for many projects by safety and industry codes.
Heat treatment is required when metal is heavily worked or rapidly heated and cooled, an example being the welding of pipes and/or pressure vessels.
Heat treatment needs to be done correctly, or it can affect your schedule.
If done incorrectly, components may become too brittle or malleable than desired, increasing safety risks and decreasing the lifespan of your workpiece. Typically, these defects present themselves during an inspection and require another application of heat treatment to be resolved. This one instance of inherited rework can add days and unaccounted-for expenses to your project schedule.
[reduce costs pullout]
Potential Schedule and Cost Issues
Your schedule could be impacted due to the limitations of your heat treatment provider’s technology and processes.
Despite their best efforts, some heat treatment vendors don’t always measure temperatures as closely as necessary. Even if temperatures are measured accurately, their monitoring system may not allow for corrective action to issues in realtime. This is often due to the technological limitations of their equipment.
Depending on the severity and complexity of the deficiency, project delays may extend weeks due to the required disassembly or cutouts of the component being heat treated. Your time-sensitive schedule doesn’t have room for mistakes that will cost you time and money.
A significant amount of your heat treatment budget goes towards idle workers.
Most heat treatment service providers invoice for idle workers due to their outdated process. Competing heat treatment providers monitor temperature cycles at the workpiece, rendering the technician useless for the duration of the time between setup and tear down. This six to eight-hour timeframe consists of a technician monitoring preheat and post weld data, which can extend even longer depending on the material specifications.
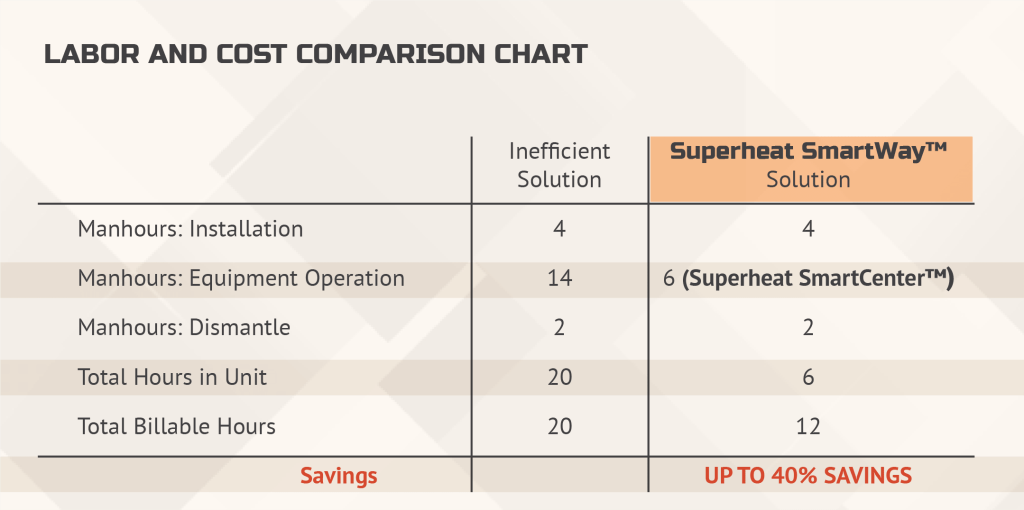
Your schedule can be delayed by a surge in demand for heat treatment.
Demand spikes for heat treatment are common on large projects as welders move forward and major components are installed. If your heat treatment service provider’s technology and technicians can’t handle the required scope, these spikes in demand can cause a tremendous backlog of work that postpones your timetable.
Solutions and Questions to Ask
Luckily, Superheat offers emerging communication technology and equipment with unique and innovative software solutions – producing the most efficient, state-of-the-art, on-site heat treatment solutions to reduce costs, save time, minimize risk and improve quality.
When vetting potential heat treatment suppliers, make sure to ask the right questions:
- How do you ensure accurate temperature measurements? Discussions of multiple thermocouples and their placement, as well as monitoring equipment, can indicate their thoroughness.
- How many thermocouples can your machines handle? This can indicate the level of technology they’ve implemented.
- What technology do you use to monitor and adjust the temperatures during the process? How detailed is the data their equipment provides? Some vendors have information that can only provide central monitoring. Ask if any issues can be handled in real-time
- What systems do you have in place to reduce idle time? Labor costs may vary significantly if they have processes in place to reduce idle workers, in comparison to having idle workers billed for an entire shift.
- Do you use remote monitoring to reduce idle labor costs? Some vendors have technology that eliminates the need for on-site monitoring completely.
- Will you offer training to my workers so they can help during crunch time? Do they offer programs to save you time and money during peak demand? Only some vendors offer this kind of training.
- Can your remote monitoring allow my trained crew to run a cycle, without your employees present? This type of program can save on costs and reduce delays due to unexpected heat treatment needs, but isn’t offered by all vendors.
You need an advanced heat treatment vendor.
Your project needs the right vendor with the best technology to detect and deal with potential issues in real-time. Your budget needs a vendor that isn’t paying idle workers, and your schedule needs a vendor that can train your staff to prevent delays in excess heat treatment demand.