Industrial oil, gas, energy, and chemical landscapes are no strangers to challenges, especially regarding the efficiency and reliability of on-site heat treatment processes. Induction heating has long been a cornerstone of maintenance, turnaround, and capital projects, offering precise and consistent heating for critical components. However, as versatile as this technology is, the experience of renting and deploying induction equipment often leaves much to be desired.
Client feedback and extensive market research have highlighted recurring pain points that negatively impact project schedules, quality, and costs. Recognizing these challenges, Superheat has broadened our offerings to include induction equipment rentals, supplemented by a robust suite of support solutions. This ensures that our clients don’t just receive tools but also the knowledge and expertise needed to succeed.
In this article, we delve into the common pitfalls of traditional induction equipment rental experiences and explore our innovative solutions that promise to revolutionize the industry. But first, let’s understand what induction heat treatment is.
Understanding Induction Heat Treatment
Induction heating generates an alternating magnetic field to produce localized eddy currents in conductive materials. Combined with the material’s electrical resistance, magnetic properties, and ferrous makeup, these currents generate heat through two primary mechanisms: Joule heating and hysteresis losses. The depth and intensity of the heating depend on factors such as the field’s frequency, coil placement, and kVA output. Induction heating can be a highly efficient alternative to traditional methods for specific scope and code parameters applications. Its precision and speed make it especially valuable.
The advantages of induction heat treatment are:
- Time to Temperature: Rapid heating allows for efficient project timelines.
- Temperature Uniformity: Induction heating creates a consistent heat-affected zone (HAZ), ensuring even temperature distribution across the component.
- Safety: Unlike traditional heat sources that involve open flames, explosive gases, or hot elements, induction heating relies on coils that remain cool during the heat cycle. This feature enhances worker safety, particularly for welders during preheating.
Watch our video above to learn how the Superheat SmartLink™ can streamline and alleviate challenges commonly faced in induction heat treatment projects.
Challenge 1: Lack of Support and Guidance
The Problem:
Traditional rental services often treat induction heating equipment, namely the Miller ProHeat™ 35, as a “drop off-and-go” offering. Equipment is delivered without adequate guidance, leaving users to figure out complex setups independently. This lack of support frequently leads to the following:
- Inefficient setup times.
- Equipment misuse or failures due to a lack of understanding of capabilities.
- Heat cycle failures that disrupt project timelines.
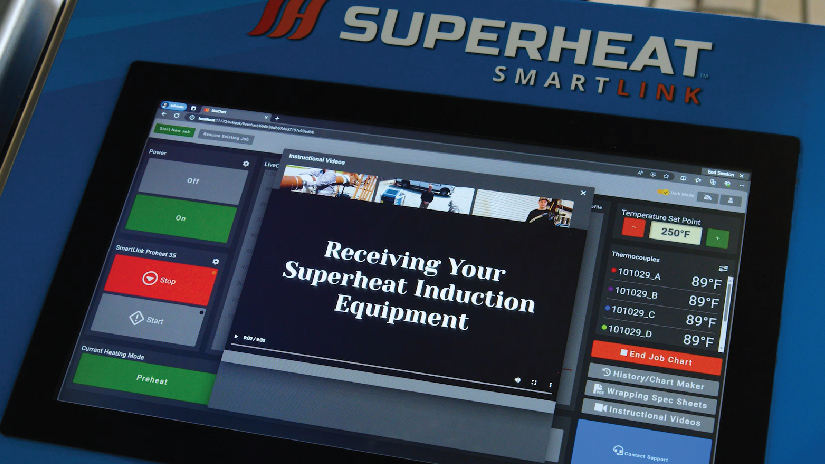
The Solution:
Superheat’s SmartLink™ platform addresses these shortcomings by providing an ecosystem of support resources:
- Tutorial Videos: A library of video guides walks users through the entire process, from commissioning Miller ProHeat™ 35 units to executing best practices for standard applications.
- Real-Time Technical Support: Should issues arise, users can connect directly with our induction experts through their SmartLink console for immediate guidance.
- On-Site Assistance: For complex issues, we will dispatch experienced service tech personnel to work directly with our clients on-site, ensuring minimal disruption to the project schedule.
The result is a significantly reduced learning curve, faster issue resolution, and a smoother overall induction heating experience.
Challenge 2: Inefficient Wrapping Techniques
The Problem:
Induction heating success relies heavily on proper wrapping techniques to ensure even heat distribution and adherence to procedural requirements. Inexperienced users often face difficulties, leading to:
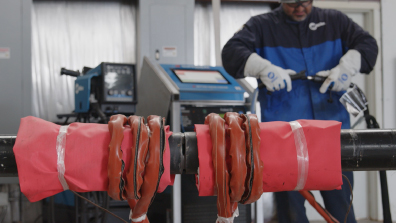
- Failed heat treatment cycles.
- Rework and project delays.
- Increased costs due to inefficiencies.
The Solution:
To combat these challenges, our engineering team has integrated technical support into the SmartLink platform:
- Drawing Library: Users have access to a comprehensive repository of standard wrapping configurations, ensuring they can replicate proven methods for reliable results applicable to their code requirements.
- Custom Solutions: Our engineering team collaborates with clients to create tailored wrapping specification sheets for unique or unconventional setups. This ensures that every project benefits from precise and effective wrapping techniques.
This proactive approach minimizes errors and maximizes the success rate of heat treatment cycles, saving our clients both time and money on their projects.
Challenge 3: Outdated and Inefficient Recording Systems
The Problem:
Many heat treatment programmers & recorders still rely on antiquated interfaces that are difficult to use and prone to user error. These systems complicate programming and data collection, reduce operational efficiency, and introduce risks to quality assurance.

The Solution:
We have modernized the programming of the Miller ProHeat™ 35 and the recording process through the SmartLink interface, offering:
- User-Friendly Design: An intuitive interface simplifies setup, operation, and data retrieval.
- Streamlined Workflow: The workflow for configuring heat cycle parameters, starting/stopping operations, and exporting data for QMS integration is designed for maximum convenience.
- Training Resources: In addition to its operational simplicity, SmartLink provides video tutorials that empower users to navigate the system confidently.
By combining modern technology with ease of use, Superheat ensures that data integrity and efficiency are never compromised.
Empowering Heat Treatment Projects with Superheat’s Expertise
The enhancements offered by Superheat extend beyond technology to transform the entire rental experience. With our tailored approach, clients enjoy improved accessibility, seamless usability, and unmatched support. These advantages translate to real-world benefits, including faster project completion, reduced costs, improved safety, and enhanced quality.
Furthermore, we at Superheat recognize that no two projects are alike. That’s why we offer flexible solutions tailored to our client’s specific needs:
- A DIY Approach with Support: Clients who prefer to manage their operations and leverage their existing staff can rely on SmartLink equipment packages for expert guidance and troubleshooting.
- A Full-Service Option: For those seeking comprehensive support, the Superheat SmartWay offering provides turnkey heat treatment solutions, including equipment, personnel, and expertise.
This adaptability ensures that every client, regardless of project scope or complexity, can access the tools and resources needed to succeed.
In an industry where time, quality, safety, and cost are paramount, the ability to address common challenges in induction heat treatment is a game-changer. Our innovative solutions, powered by the SmartLink platform, redefine what’s possible in induction equipment rentals like the Miller ProHeat™ 35 and support services.
To learn more about how SmartLink and our induction services can elevate your next project, send us a message through our Contact Us page today!