Introduction
Superheat was founded on the principles of a safer and more efficient way to provide on-site heat treatment services. Today, Superheat is leading the heat treatment industry by integrating emerging communication technology, equipment advancements, and innovative software solutions.
Through our Superheat SmartWay™ approach, control of your heat treatment process is consistent at all levels. Superheat manages on-site quality via remote monitoring technology, eliminating the need for non-productive monitoring personnel on the job site. This, in turn, reduces on-site labor requirements by up to 40% while mitigating safety concerns.
Background
Superheat performed heat treatment services during a refinery-wide turnaround for one of the largest petroleum companies in the United Kingdom. During planning stages, the project posed significant challenges as the client had a limited knowledge regarding the scope of work, due to the majority of the work being inspection-driven. This presented complications for the company’s intended work timeline during the turnaround.
Smart Solution
Implementing the Superheat SmartWrap™ program, 6 Superheat supervisors from the UK were present on-site with 24 contracted insulators. The insulators underwent Superheat’s 16-hour Heat Treatment course prior to the turnaround. Combining training with Superheat SmartCenter™ monitoring, produced further reductions in on-site labor, with Superheat remotely overseeing the process. Using Superheat SmartView™ to provide project data in real-time, technicians were able to troubleshoot heat treatment cycles in-progress while maintaining a high level of quality. The insulators were only utilized for the wrapping and stripping of welds, which accounts for 33% of the heat treatment procedure.
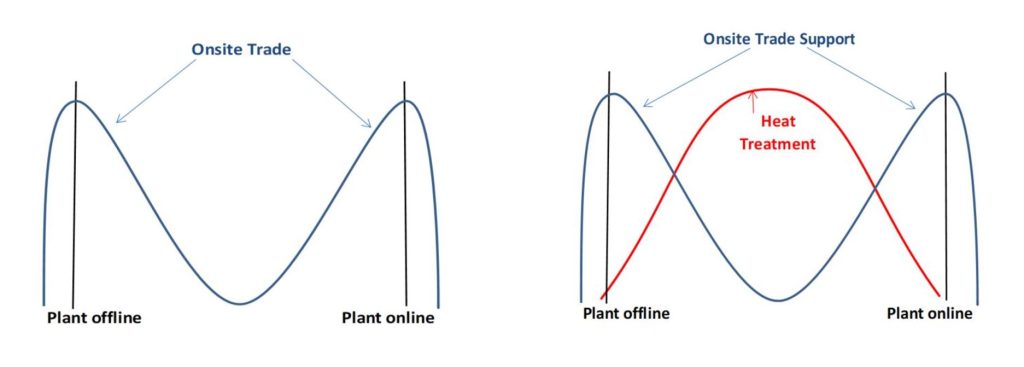
Results
By utilizing these contractors on an as-needed basis, our client obtained a labor cost savings of 36% overall. The adjusted “wrench time” for the general insulation contractor was increased by only 3%.
Weekly Manpower Savings:
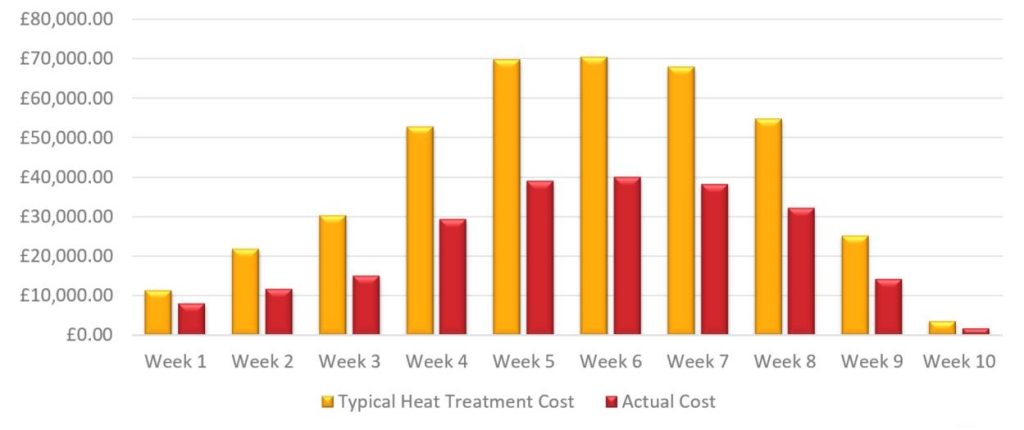
Actual Savings Summary:

The Smarter Way to do heat treatment is here.
For UK-specific inquiries, contact: +44 (0) 1462 888003