Introduction:
At Superheat, our core values focus on minimizing risk, improving quality, reducing costs, and saving time while advancing heat treatment services for the newly evolved digital marketplace. Due to the standing order of the current economic landscape, as a result of COVID-19, the margin for error has become nonexistent as cost overruns and schedule backlogs result in greater catastrophic impacts. Therefore, when an international contractor in Abu Dhabi required the world leader in heat treatment to service their DRP Units 1 and 2 Solution Annealing needs they called upon Superheat to implement our advanced heat treatment services and digital applications. However, the global pandemic intensified, and travel restrictions broadened, eliminating the traditional method of positioning Superheat Project Managers and Field Technicians directly to the clients work site. Superheat and their innovative thinking prevailed by understanding and identifying the true needs of the client and applying dynamic solutions that aligned with the current economic and environmental circumstances.
Scope:
DRP Units 1 & 2 had various Vertical Tube Ends, U Bends, and intricate Cross Over sections requiring solution annealing heat treatment. The outage also consisted of 20+ Joints that posed several obstacles during the setup and tear down of wrapping configurations.
The Superheat SmartWrap™ Solution:
Staying true to the notion of “advancing heat treatment for the digital marketplace”, Superheat knew they could remotely operate their heat treatment equipment from the Superheat SmartCenter™ and digitally manage Quality Assurance if they could train the contractors laborer’s virtually. This would include training on the comprehension and practical implementation of a solution anneal technical procedure (TP) in combination with the usage of Superheat SmartView™.
Superheat SmartView™ is a quality management app that enables field staff to interact directly with the Superheat SmartCenter™ to exchange quality related documents all while presenting real time operational data such as Live Heat Cycle charts and Weld Statuses. Consequently, that’s just what Superheat proposed. “The SmartWrap™ service offered provided our extensive quality program and expert knowledge base of heat treatment while leveraging the contractors own labor force”, explained CEO Norm MacArthur.
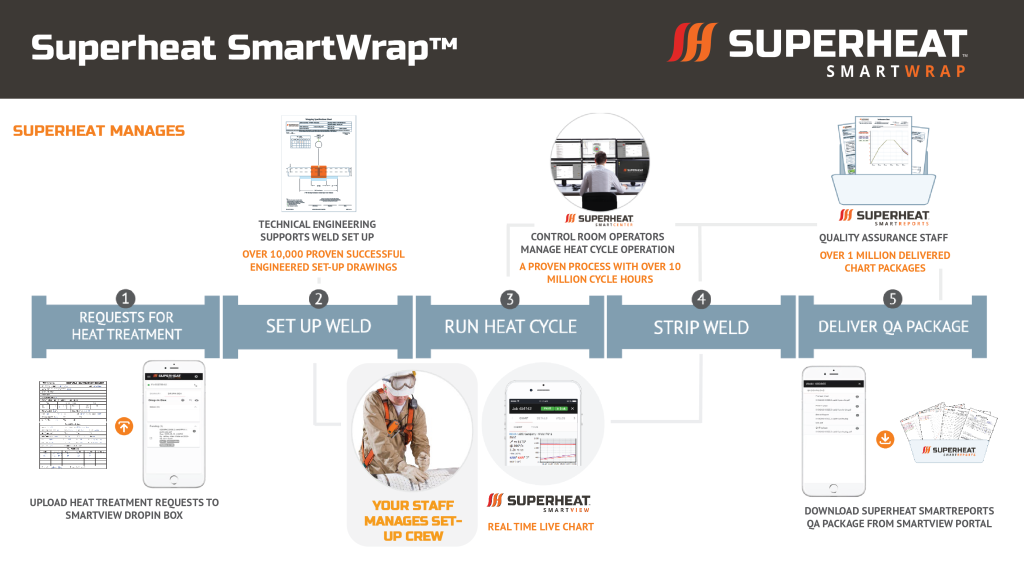
After shipping Superheat SmartPoint™ heat treating consoles and job site consumables to the Abu Dhabi facility, the United Kingdom division of Superheat got to work organizing pre-outage virtual training with the contractors handpicked labor group that now acted as a site-specific heat treatment division. The elaborate zoom training meetings consisted of multiple live camera streams and mock-up piping that replicated in service components that required heat treatment. This allowed the clients staff to practice and simulate specific heat-treating skills while receiving instant verbal and written feedback from the live video Superheat trainer. Through multiple class like virtual training sessions and mockup run throughs Superheat developed, enhanced, and tested the client’s comprehension and proficiency of skills. These heat treatment skills included surface preparation, strong thermocouple attachment and labeling practices, proper electrical resistance pad installation techniques in alignment with engineered wrapping specifications, insulation placement and banding, and overall cable connection and management.
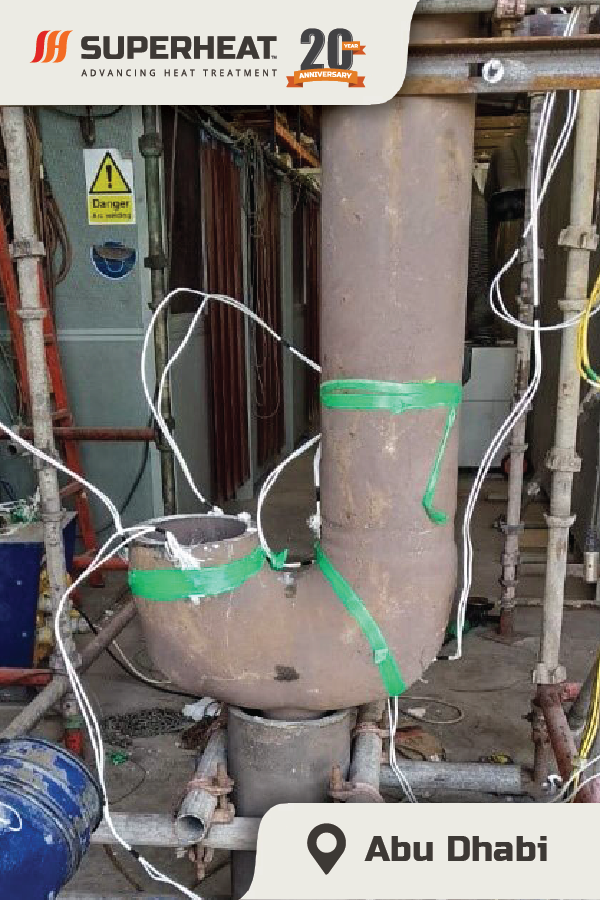

Once the client demonstrated efficiency in managing the heat treatment set up, live virtual tutorials continued with regards to hot strip procedures that are a critical step in air quench solution anneals. A major emphasis was placed on safety protocols and the proper usage of PPE equipment. Beginning with securing a “safe zone” with adequate insulation protection and explaining that suitable barriers and signage was needed to produce a controlled environment. The Abu Dhabi team was then walked through via video conference the process of safety locking out and disconnecting cabling which further led to a demonstration of the controlled removal of insulations, heating elements, and proper placement of forced Air fans.


The final element of training revolved around the usage of Superheat SmartView™. Teaching the site staff, through collaborated screen sharing, to utilize the Drop-In box feature within the app to uploading completed wrapping specifications sheets. This confirmed the Superheat SmartCenter™ remote operators were aligned on wrapping configurations of the component and project schedule requirements. The clients labor crew was also introduced to Live Chart section of SmartView™ which provides a real-time heat cycle chart with key pieces of supplemental data such as estimated completion time and weld stage indicators. This enabled the site staff to prepare for next steps and improve project efficiencies. The last component of the demonstration was the QA package download segment of SmartView™ where all QA document packages related to the weld, primarily charts, are stored for download. The Abu Dhabi quality team was now able to streamline record keeping with their primary enterprise system.

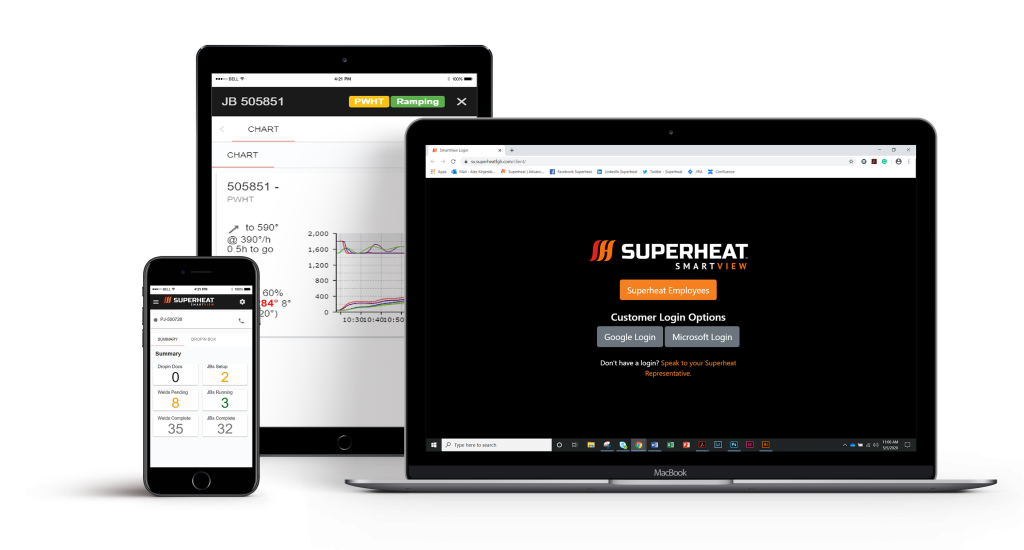
All stages of the live video training had now been delivered and the site crew had performed and satisfied all practical mock up evaluation requirements. It was now time for the actual outage heat treatment applications.
Results:
After 11 days of intensive digital training supplied from Superheat’s Management the clients newly formed on-site heat treatment team in Abu Dhabi successfully overcame their site-specific obstacles to complete a turnaround on DRP Unit 1 & 2. By learning how to properly self-perform the heat treatment at hand, utilize Superheat’s digital QA platform Superheat SmartView™, and take advantage of the support from the Superheat SmartCenter™ as they remotely operated heat cycles all welds were completed with 100% success rate. At the completion of the project the Global Service Center, Head of Asset Management for the Abu Dhabi Executive Team presented Superheat an excellent customer satisfaction report. Rating Superheat’s sales support, scope definition, input, equipment, personnel, attitude, timeliness, response to project changes and productivity as “superior”. When asked about the virtual training he noted “Excellent support from the Superheat team during the tricky COVID period. A Special thanks to the UK QA/HSE manager Stephan Guy for the remote support”.