Introduction:
Superheat was founded in 2000, a time when the on-site heat treatment industry was not practicing high-standard safety procedures, and equipment posed unnecessary risks to those in the workforce. Throughout the last 23 years, Superheat has focused on safety standards that do not compromise cost or quality to our clients and customers. Through our on-site heat treatment equipment, remote operations, internal programs, and digital advancements, we have innovated safety in our organization and become leaders within the industry.
The Superheat MagneMat™ Equipment Safety Advancement:
Resting on laurels and using traditional equipment and procedures are commonplace among oil and gas contractors. Operating expenses associated with research and development coupled with a reluctance towards change generally reduce the focus on innovation. However, over several years, Superheat has
invested significant experimentation into magnet technology that has forever changed the design and installation methods of flexible ceramic heating pads. This groundbreaking advancement has created a waterfall effect of risk minimization across many disciplines on any given job site.
We have put a procurement priority on magnets in which their electromagnetic field are minimally affected by standard preheat and PWHT temperature parameters on large vessel and big bore piping applications. Integrating magnets into the traditional ceramic pad heater has created the new Superheat MagneMat™, which eliminates the requirement for pins during the preheat and PWHT setup process entirely. This innovation removes inherited risk events from the standard SOP, such as pre-vessel mapping, pin installation and removal that require pre/post grinding, NDE (nondestructive testing), and extensive quality management measures. By negating these steps while maintaining a heightened standard of quality and efficiency, the Superheat MagneMat has dramatically reduced risk to the onsite
heat treatment scope and to additional parties involved in the overall life of a weld. Click here to read how PBF Martinez refinery utilized the Superheat MagneMats to alleviate the need to attach, grind off, and inspect 540 pin locations on two coke drums.
Superheat’s Innovative Safety QR Code Portal & Metrics:
The paperless revolution is not only a step toward sustainability but also enhances the responsiveness in which an individual can submit and access real-time safety information. In our mission to be the “Better.Safer.Faster” on-site heat treatment provider, we recently shifted the traditional paper method of safety documentation for a novel QR code-accessible digital safety portal. We now enable our field and site management staff to electronically submit SWAT (Safe Work Action Team) observations, Incident Reports, and access Safety individual contact information from any device at any time, from anywhere.
The SWAT submittal process actively promotes the ongoing involvement of employees through observations of their peers while they perform day-to-day tasks within their scope of work. Observation data is now documented on a digitally submitted SWAT form compared to the primitive handwritten card method, which was manually tracked and physically organized. Employee teams have monthly meetings to discuss their activities, trends, ideas, and recommendations to improve the safety process and address any issues.
The primary objectives of the SWAT are:
- Excel in safety – be the best.
- Recognize and reinforce safe behaviors.
- Have the ability to recognize and eliminate “At Risk” behaviors with immediate intervention.
- Create a safety culture focused on improving behaviors before an incident or accident.
- Utilize the SWAT data to develop injury prevention initiatives and reward successes.
- Incorporate trust among coworkers to keep watch on one another without questions or reprimand.
- Promote ownership of the process and active employee involvement. Field Technicians at all levels are encouraged to promote the identification of at-risk behaviors so that they can be eliminated from the work areas through feedback and intervention.
The number of digital submissions per individual each month is tracked and the recognition of participants is categorized as either Level 3 (Participant – under 4 SWAT cards submitted), Level 2 (Silver User – 4 SWAT cards submitted), or Level 1 (Smart User – 5 or more SWAT cards submitted). Monthly submitters from the categories are added to a pool, and SWAT members then choose two quarterly winners. Awards, such as gift cards, are chosen by the winners and can be utilized to impact their families. The eight quarterly winners are then eligible for the annual award chosen by SWAT members. The annual award will have a $500 maximum value and all winners are recognized via the company safety newsletter and selected social media platforms.
Since the transition in June 2022 from physical SWAT cards and incident reports to digital submissions, participation and involvement in the overall initiatives has risen by 15% month over month. This digital safety innovation has enabled employees to efficiently and conveniently communicate events that could otherwise go unreported due to the elongated method of physical form completion and management organization.
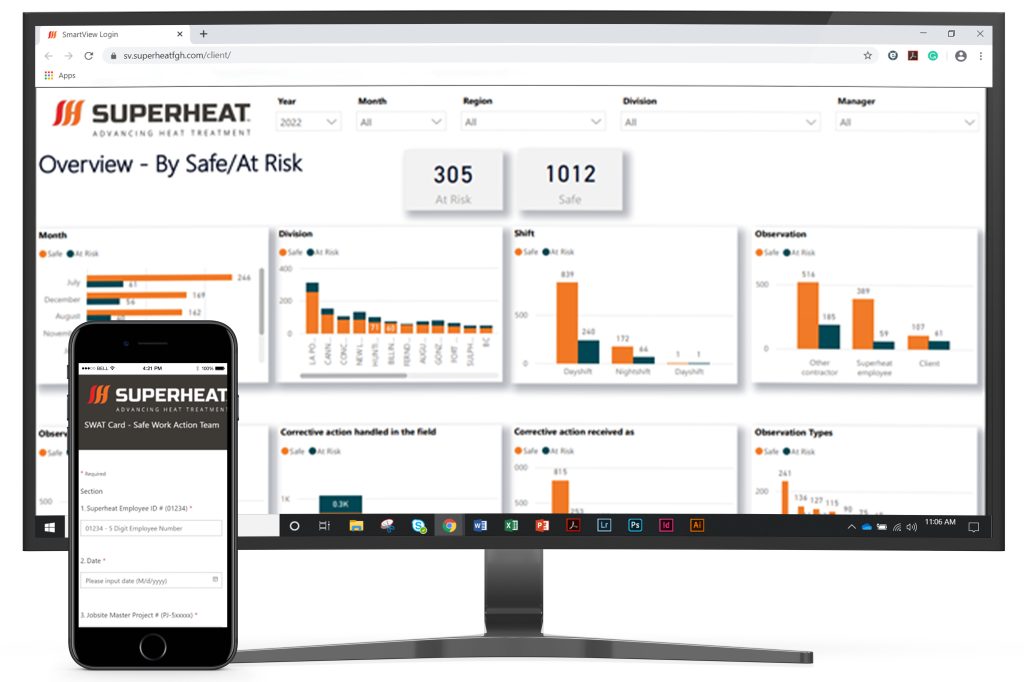
Superheat SmartView™, our overall project management app, also provides instant access to various safety resources, including site-specific safety protocols, access lessons learned, review PPE requirements related to their scope, manage PAR (personal accountability rosters) per job site, and even review approved drivers lists. This interactive platform gives site management the tools and knowledge directly at their fingertips to create a safe working environment for their field team members. Additionally, the document upload feature in SmartView enables site-level managers to share daily tailgates and exchange other pieces of critical information pertaining to our safety programs. This data is audited at the regional and national levels during KPI meetings. Should negative or positive trends be found, corrective actions and/or improvements are built into procedures. This proactive approach to the collection, distribution, and analysis of safety data is made possible through digital innovation. The result profoundly affects our ability to maintain the highest industry safety standard in relation to key metrics such as EMR, TRIR, LTI.
SmartCenter™ & SmartPak™/SmartCard™ Safety Features:
At Superheat, we are the only company in the world dedicated to the true remote operation of on-site equipment from our centralized off-site Superheat SmartCenter™. Through a patented process that integrates remote operation technology and equipment advancements, we provide an on-site heat treatment service in which 100% of the equipment and heat cycles are controlled remotely. Compared to the industry standard, Superheat reduces the required man-hour footprint on job sites by up to 40%, thus decreasing the headcount through clients’ gates and ultimately removing field staff from potentially hazardous areas. In 2022, we renewed our commitment and belief in the remote monitoring approach with a complete rebuild of the Canadian, United States, and soon-to-be United Kingdom SmartCenters. Upgrading all hardware and expanding the number of pod locations to align with growth in market share to ensure our operators have access to the best computing equipment available.
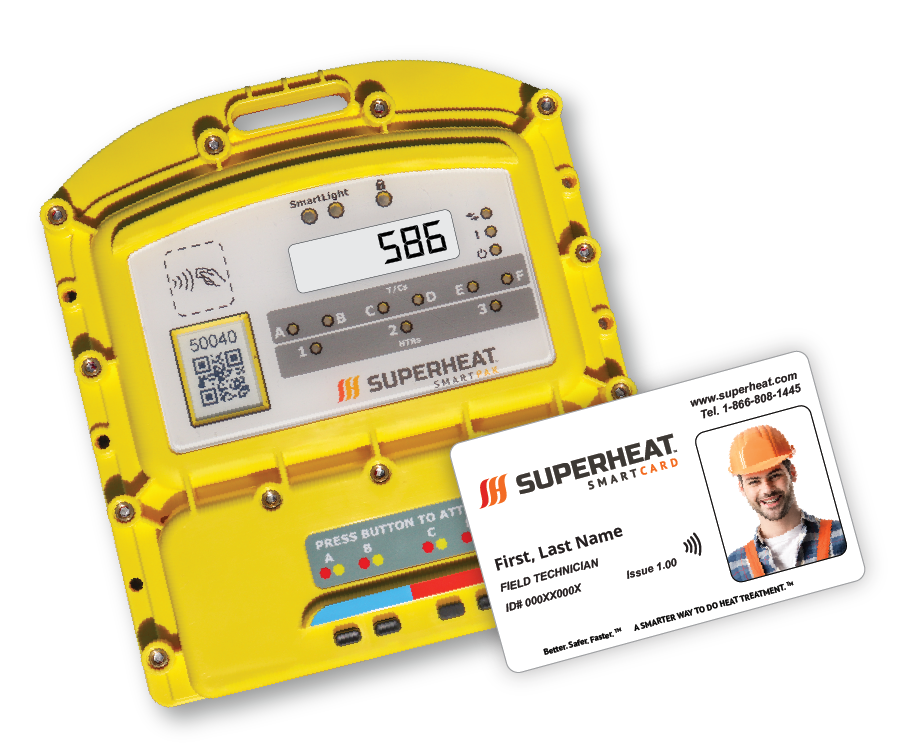
Furthermore, the Superheat SmartPak™ is the only piece of equipment in the industry to provide safety lock-out capability directly at the component location to minimize the risk of electric shock to field personnel. Upon completing standardized training, each technician receives a personalized Superheat SmartCard™, which utilizes nearfield technology when swiped at the Superheat SmartPak™ to lock out power to designated components immediately at the work location. This puts control over safety directly at the individual level and removes the need for staff to leave the work area to isolate the power of the equipment consoles, as they can be far distances away from the component being heat treated. The swipe of this card to the Superheat SmartPak™ also indicates to our panel operators that they can safely start the heating process and that the weld area is in a safe condition to proceed.
Conclusion:
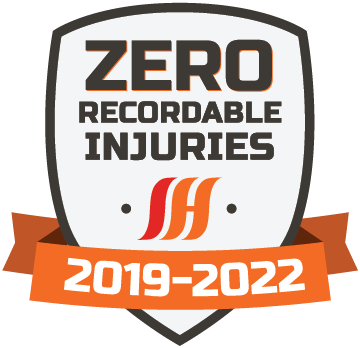
We feel each incremental innovation, no matter how small, has impacted the overall safety of the environment in which our team members work and the corresponding metrics which result. Each member of the Superheat Team has played a key role in making safety our utmost priority day in and day out. 4 consecutive years of Zero Recordable Injuries have primarily been made possible through the outstanding dedication of our boots on the ground and by our Regional Safety Representatives Emily Switzer, Bret Cadenhead, Joe Brynda, Ian Rezac, Tony McDonald, and Stephen Guy and their synergy with Superheat’s operations Teams. Four years, in reality, represents thousands of excellent daily safety decisions that every member of our Team has made in some way, shape, or form to achieve this milestone. When faced with any performance or production challenge versus taking the safe path – the results are clear – our Team takes pride in our safety-based culture, and this achievement speaks volumes in our industry.
United States Safety Statistics:
Variable | 2020 | 2021 | 2022 | 3 Year Avg. |
---|---|---|---|---|
Experience Modification Rate (EMR) | 0.55 | 0.56 | 0.59 | 0.56 |
EMR – California | 0.44 | 0.44 | 0.48 | 0.45 |
EMR – Michigan | 0.95 | 0.95 | 0.95 | 0.95 |
EMR – Pennsylvania | 0.859 | 0.86 | NQ | 0.86 |
Total Recordable Incident Rate (TRIR) | 0 | 0 | 0 | 0 |
Loss Time Injury (LTI) | 0 | 0 | 0 | 0 |
Canada Safety Statistics:
Variable | 2020 | 2021 | 2022 | 3 Year Avg. |
---|---|---|---|---|
Total Recordable Incident Rate (TRIR) | 0 | 0 | 0 | 0 |
Loss Time Injury (LTI) | 0 | 0 | 0 | 0 |
United Kingdom Safety Statistics:
Variable | 2020 | 2021 | 2022 | 3 Year Avg. |
---|---|---|---|---|
Date Away Restricted or Transferred (DART) | 0 | 0 | 0 | 0 |
Reporting of Injuries, Diseases & Dangerous Occurrences Regulations (RIDDOR) | 0 | 0 | 0 | 0 |